The Transition to Fluorine-Free Foams in Fire Protection
- thekuljeet
- 4 days ago
- 4 min read
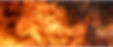
Introduction
Foam-based fire protection systems have been a cornerstone of industrial fire safety, especially for high-hazard areas like fuel storage, aviation facilities, and chemical plants. Traditionally, aqueous film-forming foams (AFFF), containing fluorinated compounds (PFAS), were the industry standard due to their exceptional performance in quickly extinguishing flammable liquid fires. However, evolving environmental concerns and tightening regulations are driving a global transition toward fluorine-free foam solutions. This article summarizes the technical, regulatory, and practical aspects of this transition.
Foam systems are used in multiple applications: flammable liquid storage (NFPA 30), aviation (closed sprinklers, deluge systems, high-expansion foam), fuel loading areas, parking garages, and diesel generator fuel storage. These systems are governed by standards such as NFPA 11 (foam systems), NFPA 13 (sprinklers), and NFPA 409 (aircraft hangars). Notably, as of the 2021 edition, NFPA 11 has absorbed the requirements of NFPA 16.
Foam works by forming a barrier between fuel and oxygen, smothering flames, and cooling the fuel surface. Foam concentrate is mixed with water to create foam solution, which is then aerated through discharge devices (often sprinklers) to produce the protective foam blanket.
Technical and Regulatory Drivers
Historically, foam evolved from early chemical foams (based on CO2 bubbles) to protein foams (derived from animal byproducts), synthetic foams, and eventually AFFF, which introduced fluorinated surfactants for superior film formation and performance. AFFF became the gold standard after military incidents, like the USS Forrestal fire, demonstrated the need for highly reliable suppression of jet fuel fires. However, these fluorinated compounds fall under the PFAS family, which includes thousands of persistent and bioaccumulative chemicals now facing regulatory scrutiny worldwide.
The U.S. Environmental Protection Agency (EPA) launched the PFOA Stewardship Program in 2010 to phase out specific fluorinated substances, but by extension, the entire class of PFAS chemicals has come under restriction. Drinking water regulations now target PFAS at levels as low as four parts per trillion—a concentration equivalent to one second in nearly 8,000 years or one drop in five Olympic-sized pools. This regulatory pressure has forced manufacturers to innovate fluorine-free foams (F3), which intentionally exclude PFAS.
Fluorine-free foams, also called synthetic fluorine-free foams (SFFF), began development around 2010, with the first alcohol-resistant formulations emerging in 2014. While these newer foams avoid PFAS, they face performance challenges. AFFF's film formation accounts for 85-90% of its fire suppression efficiency, so F3 foams must compensate with denser bubble structure, requiring higher application densities.
Practical Considerations for Transitioning Systems
Equipment compatibility is a key consideration when transitioning systems. The core components of a foam system include bladder tanks, proportioners (ratio controllers or variable range proportioners), and discharge devices like sprinklers or foam chambers. Bladder tanks work using a balanced pressure principle, where water squeezes the internal bladder containing the foam concentrate, forcing the concentrate into the proportioning system. Older systems designed for AFFF may not match the flow ranges or application densities required for F3 foams, making simple concentrate swap-outs insufficient.
For instance, systems using K-8 sprinkler heads previously designed for AFFF at 0.3 gpm/ft² may require F3 foams to operate at 0.37 gpm/ft² or higher. This translates to increased system flow rates, larger bladder tank capacities, and possible upgrades to proportioners or sprinklers. Additionally, any component that has contacted raw AFFF concentrate (like the bladder material, proportioning devices, or concentrate piping) should be replaced to avoid PFAS contamination of the new foam.
Two major fluorine-free foam products highlighted are Re-Healing RF3 (for hydrocarbon fuels) and Re-Healing 3x3 SP100 (for both hydrocarbons and polar solvents), both offering UL listings and FM approvals. Notably, UL testing uses a 12'4" x 12'4" sprinkler grid, while FM uses a tighter 10'x10' grid with both high- and low-height tests, adding complexity to performance validation.
Changing from AFFF to F3 is not a one-size-fits-all process. For existing systems, factors like application density, system hydraulics, and local jurisdictional requirements (set by authorities having jurisdiction, AHJs) all influence the retrofit process. Environmental regulations vary across states, so collaboration with local and state environmental agencies is critical. In some cases, entirely new systems or piggyback tanks may be needed; however, balancing parallel systems adds operational complexity, so the preferred approach is often upsizing existing equipment.
Operationally, F3 foams may have higher biological oxygen demand (BOD) and different environmental disposal requirements. Disposal of legacy AFFF should always follow local environmental agency guidance, as contamination risks are tied to ultra-low PFAS thresholds.
System designers, installers, and facility owners should approach the transition holistically, viewing foam systems as an integrated kit: bladder tank, concentrate, proportioner, and discharge device must all work together and maintain the necessary UL or FM approvals. While hydrocarbon-only systems may see simpler transitions, facilities with polar solvent hazards (such as alcohols) must carefully account for higher density requirements.
In summary, the transition to fluorine-free foams reflects a critical evolution in fire protection, balancing performance needs with environmental and health imperatives. While the technical challenges are nontrivial, modern F3 formulations, combined with careful system evaluation and adherence to regulatory standards, enable facilities to maintain robust fire protection without relying on PFAS chemistries.
Stakeholders are encouraged to engage early with manufacturers, environmental regulators, and testing agencies to ensure successful, compliant transitions. The future of foam-based fire protection lies in solutions that are both effective and environmentally responsible—and with advancing technology, that future is within reach.
For any further inquiries regarding this topic, as well as for code consulting and fire engineering design support related to your project, please don’t hesitate to contact us via email at contact@engineeringfireprotection.com.
Application of any information provided, for any use, is at the reader’s risk and without liability to Engineering Fire Protection (EFP). EFP does not warrant the accuracy of any information contained in this blog as applicable codes and standards change over time. The application, enforcement and interpretation of codes and standards may vary between Authorities Having Jurisdiction and for this reason, registered design professionals should be consulted to determine the appropriate application of codes and standards to a specific scope of work.